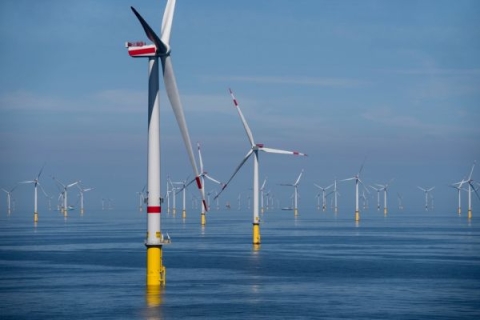
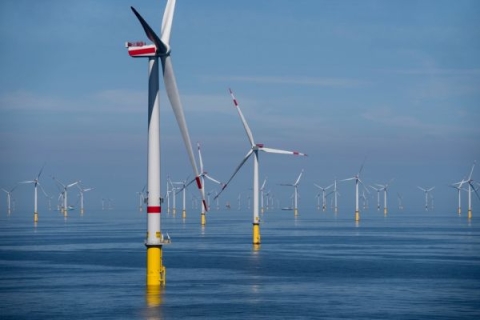
New £1.6 million project to develop an autonomous fleet of drones for offshore wind farm inspection.
15 March 2021
5 min read
A swarm of drones might soon take the place of humans dangling on a rope to do routine close-up safety inspections of offshore wind turbines.
When a technician inspects a wind turbine, the blade must be stopped in the six o’clock position and a technician is lowered down from the top on ropes or cables. They then test the blade using their hands or knees to knock, looking for weak spots or damage.
The work is not only highly dangerous for humans – it’s also not as efficient as using sensors mounted on drones, which can inspect an entire offshore wind farm of more than 100 turbines in a fifth of the time.
Delivered by the University of Portsmouth in partnership with Airborne Robotics, Bentley Telecom and Ocean Infinity, the £1.6 million project aims to develop an autonomous offshore wind farm inspection fleet consisting of unmanned drone swarms and a marine robotic vessel by 2022.

Ultimately, we are aiming to develop a system that can detect and monitor defects or damages inside the turbine and the entire structure of a wind turbine in a safe and effective way.
Dr Sarinova Simandjuntak, Senior Lecturer, School of Mechanical and Design Engineering
The project, Drone Swarm for Unmanned Inspection of Wind Turbines (Dr-SUIT) is funded by the Future Flight Challenge programme from UK Research and Innovation (UKRI) and the Industrial Strategy Challenge Fund.
Offshore wind currently powers the equivalent of 4.5 million homes annually and generates nearly 10 per cent of the UK’s electricity making the UK the world leader in offshore wind energy.
Dr Sarinova Simandjuntak, from the School of Mechanical and Design Engineering, is the University’s Principal Investigator. She said: “Offshore wind turbines will soon be far taller than Portsmouth’s Spinnaker Tower as new ones being built are up to 180 metres high. As they are also located in the middle of the ocean, maintenance and repair can be challenging. Blade damage caused by lightning strikes or gale force winds, for example, can be easily missed.
“Ultimately, we are aiming to develop a system that can detect and monitor defects or damages inside the turbine and the entire structure of a wind turbine in a safe and effective way. This will benefit offshore wind farms, reducing the time they have to shut down for maintenance and therefore increasing availability and supply.”
The project will use 5G, satellite connectivity and an unmanned ship to enable a swarm of drones to autonomously inspect the wind turbines, preventing any risk to humans. It will also apply and test cosmic rays to scan the turbines for damage inside and out.
Currently manual inspections take 12 technicians who can cover between two to five turbines a day. Using a swarm of drones could potentially cut inspection time from five weeks to one week and could cut costs by 50 percent.
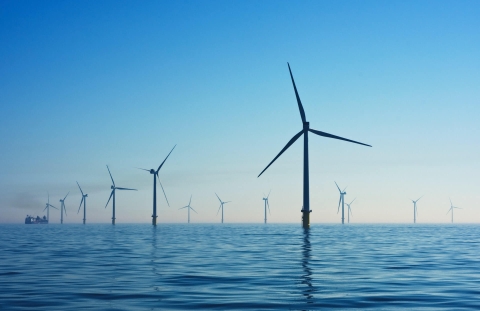
Offshore wind turbine maintenance and repair can be challenging.
The drone swarm will be connected using 5G technology hosted on one of Ocean Infinity’s 36 metre ‘Armada’ uncrewed marine vessels, which will also host battery recharging docking stations. Drone data will be collected on the platform and then relayed via satellite, before being processed and stored on the University’s supercomputer.
The project will examine hovering time, flying time, wind conditions, collision avoidance and the power consumption of on-board equipment in order to determine the most efficient and cost-effective drone swarm configuration for inspecting an entire wind farm – some of which have over 100 turbines.
Dr Simandjuntak said: “This project will allow us to implement some impressive technology and latest research, such as 5G and satellite technology for fast and large data relay.”
The university team includes Professor Djamila Ouelhadj who is leading on the drone swarm operational platform supported by Dr Xiang Song, Professor Victor Becerra who is leading on battery health management and Dr Andy Gibson who is leading on structural integrity analysis.
The team is planning its first live demonstration of the drone swarms this summer at a wind farm off the coast of Essex.
Minister for Business, Paul Scully, said: “We’re investing in ambitious projects, like Dr-SUIT’s remote drone technology, to ensure the aviation industry is championing the latest cutting-edge technology.
“Pioneering research supported by government funding will help the UK build back greener from the pandemic, remain at the forefront of aerospace research and development, and demonstrate global leadership in the next aviation revolution. I look forward to seeing the project take flight.”
The project has also been supported by the South Coast Centre of Excellence for Satellite Applications. Louise Butt, Business Development Manager, said: “Satellite technologies continue to play an essential role in the continued roll-out of remote sensing and autonomous systems, providing the necessary infrastructure for unmanned technology deployment. With the UK's ever-growing reliance on renewable energy, we see the wind-farm sector as a major beneficiary with increased productivity and minimised human intervention as a result of these space assets.”
Once the project has been rolled out, it is hoped that drone swarm inspection can be used in other sectors such as oil and gas, forestry, solar and mining.