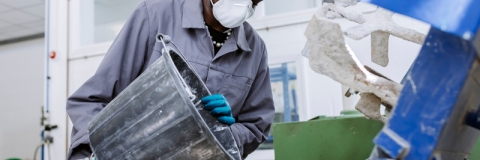
Sidebar navigation
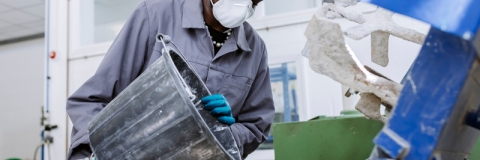
Containment Levels
Facilities design, safety equipment and working practices.
Introduction
Activities involving biological agents or entetic modification, are carried out in specially designed laboratories. These are described in COSHH as Containment Levels (CL). The requirements for the four different containment levels (CL1, CL2, CL3, CL4) are a combination of facilities design, safety equipment and working practices. As the CL number increases the level of control also increses.
Biological hazards must be handled in the minimum containment level to their risk, for example hazard group 1= containment level 1. Hazard group 1 can be handled in containment level 2, but hazard group 2 can not be handled at containment level 1.
The University has both containment level 1 and 2 facilities, the exact containment level required depends on the work, the minimum control measures are listed below for containment level 1 and 2.
Containment Level 1
Introduction
Containment level 1 is used for work with low risk biological agents and hazards, genetically modified organisms, animals and plants. This guidance is a summary of some important controls used for work in containment level 1 laboratories but is not exhaustive and you will need to do other things as well depending on your specific work and risk assessments. It is not intended to describe all of the necessary control measures and more information on controls can be found on the SEPS, HSE and DEFRA websites.
Protocols and Risk Assessment
- There must be adequate policies, local rules, risk assessments, controls and standard operating procedures for the work.
- Managers and principal investigators are responsible for health and safety management, risk assessment and control.
- All workers and visitors have health and safety responsibilities.
- Risk assessments must be carried out where they are required including general risk assessments, COSHH, Biological COSHH and GM risk assessments.
- Biological COSHH risk assessments will help you identify the biological hazards, evaluate the risks and decide on appropriate control measures to enable you to do the work safely and reduce the risks of accidents.
- All workers and visitors must have adequate information, instructions, training and supervision.
- Managers and principal investigators must monitor activities to ensure risk assessments, controls and standard operating procedures are implemented and effective.
- Risk assessments, controls and standard operating procedures must be reviewed and amended where there are significant changes to the activity or risks.
- Managers and principal investigators must keep risk assessments, standard operating procedures and other important records.
- There should be adequate communication and cooperation between users of shared laboratories and facilities in relation to the hazards, risks and control measures required to protect health and safety.
- Key standard operating procedures and emergency procedures should be displayed in the laboratory.
- Health, Safety and Wellbeing Coordinators, Biological Safety Supervisors, Bioloigcal Safety Officer and Corporate Health and Safety are available to provide advice and support on health and safety management.
Signage and Security
- Relevant safety signs should be placed on laboratory doors (eg biological hazards, chemical hazards, radiation hazards, containment level, flammables and gas cylinders).
- Safety signs which should be on laboratory doors for containment level 1 laboratories include (a) authorised persons, (b) biological hazards and (c) containment level 1.
- Laboratories should be locked when not in use or unoccupied.
- Access should be restricted to only authorised persons.
- Visitors and contractors must be adequately supervised.
- Access to laboratories must be controlled using suitable means (eg lock and key, swipe card, digital lock etc).
General Safety
- Surfaces of benches, floors and walls should be impervious to water, easy to clean, resistant to acids, bases, solvents and disinfectants.
- Benches should be constructed of robust material (eg Trespa) using non-shrink sealants (eg Silicone or Epoxy resin).
- Adequate space and light should be provided for each worker.
- Procedures that produce hazardous or infectious aerosols must be adequately contained (eg equipment, safety cabinets, centrifuges, shakers etc).
- Microbiological safety cabinets should be used for work where hazardous or infectious materials aerosols could be produced.
- Centrifuges should have sealed buckets or rotor which can be opened inside safety cabinets.
- Fume cupboards should be used for work with hazardous chemicals.
- Laboratory ventilation and safety cabinets should be regularly inspected, maintained and tested usually at least every year.
- Lone working should be avoided but if there is no alternative then adequate controls must be used including supervision, active monitoring and the use of lone worker monitor/alarms.
- Avoid use of sharps unless really required and then adequate risk controls should be used.
- Avoid generating aerosols.
- Biological agents and hazards, genetically modified organisms, animals and plants should be safely and securely stored.
- Multiple containment should be used for storage of hazards.
- Biological agents and hazards and genetically modified organisms should be safely and securely transported.
- Multiple containment should be used for transport of hazards.
- Use suitable robust containers and label accurately for internal transport in and between buildings and where necessary use trolleys and spills kits.
- Use correct UN approved packaging containers, labels and protocols for external transport.
- Disinfect equipment and working surfaces after use where required.
- Do not store or consume food or drink in laboratory.
- Do not store outdoor clothes or bags in laboratory.
- Good personal hygiene practices are necessary in laboratories.
- Cover cuts and broken skin with waterproof dressings.
- Handwash sink with an emergency eyewash hose should be near to all exit doors.
- Taps should operate without being touched by hand.
- Soap and paper towel dispensers should be provided.
- Emergency eyewash hose should be provided which can be used for cleaning eyes, mouth or body in case of personal contamination by any hazards.
- Wash hands after completion of work activities and immediately after any contamination is suspected or handling hazardous materials.
Sharps
- Avoid the use of sharps unless they are essential since sharps can cause serious injuries and exposure to biological hazards and other hazardous substances.
- Think and plan carefully how the work can be done to reduce the risks of exposure and sharps injuries.
- Use safe techniques when using sharps.
- Use alternative safety sharps where possible if you can (eg syringes with retractable needles and scalpels with retractable blades).
- Use forceps to hold tissues or materials.
- Use blunt instead of sharp needles, scissors and forceps.
- Use core borers instead of scalpels if possible.
- Do not hold materials with hands unless there is really no alternative and it is essential.
- Use forceps or clamps to hold materials when cutting etc.
- Keep the other hand without the sharp as far apart as possible from the hand holding and using the sharp to reduce the risk of stab or cut injuries.
- Generally the further apart your two hands are the less likely you are to injure yourself in a sharps accident.
- Do not pass or transfer used sharps to other people.
- Do not re-sheath needles.
- Store sharps where necessary in solid boxes to prevent contact with them causing injuries.
- Do not leave your sharps lying around since they can injure you and other people and cause accidents.
- Dispose of waste materials carefully and using the correct route.
- Dispose of sharps immediately after use.
- Use puncture resistant sharps bins to dispose of used sharps.
- Take the sharps bin to the sharps not the other way around.
- Put the sharps bin where you are going to use the sharps.
- Lock the lid onto the sharps bin before use and do not overfill sharps bins.
- Do not push objects or fingers into opening of the sharps bin.
- Disinfect spills immediately.
- Disinfect or sterilise equipment and work surfaces after use where needed.
- Use personal protective equipment (eg lab coat, gloves, specs, goggles or face shield etc).
- Use double gloves.
- Kevlar or chain mail gloves can offer useful additional protection for some activities.
- Wash your hands after the work is completed.
Personal Protective Equipment (PPE)
- Appropriate personal protective equipment (PPE) should be used where required.
- PPE is often essential for many aspects of work but generally only as additional rather than the main method of protection.
- Suitable laboratory coats should be used.
- Suitable gloves should be used where required.
- Suitable spectacles, goggles or face shields should be used where required.
- Specialist gloves can be used for specific biological, chemical and physical hazards (eg cut resistant Kevlar or chain mail gloves).
- Disposable clothing (eg overalls, overshoes, caps, gowns and masks) should be used where required.
- Boots, shoes, aprons, visors should be used where required.
- Gloves should be worn for all work with hazardous or infectious materials.
- Gloves should be used with care to prevent contamination of materials, surfaces and equipment.
- Gloves should be removed and disposed if they become contaminated.
- Respiratory protective equipment (RPE) should be used where required but must be properly selected, inspected, maintained and tested.
- RPE should not be used as an alternative to more effective control measures.
- PPE should be removed before leaving work area and kept apart from normal clothing.
- PPE should be stored in a defined place, kept clean, maintained and cleaned at suitable intervals.
Waste Management
- Waste should be properly labelled, safely handled, stored, transported and disposed.
- Waste should be properly inactivated using a validated means before disposal.
- Waste bags and sharps bins should not be overfilled.
- Dispose of waste safely using appropriate containers and correct waste route (eg waste bags or bins, sharps bins, hazardous or non-hazardous waste, biological, chemical or radioactive waste etc).
- Validation and monitoring of effectiveness is required to prove that inactivation method works.
- Effective disinfectants should be available.
- Disinfectants should be suitable for the biological agents and hazards, genetically modified organisms, animals and plants used in the work.
- Check manufacturer’s instructions and validation of effectiveness of disinfectants.
- Regular decontamination of surfaces of safety cabinets and benches is required.
- Autoclaves should be accessible in the building.
- Laboratory autoclaves should be inspected, maintained and tested at least every year.
- Validation of effectiveness is required for autoclaves using annual thermocouple testing of standard loads.
- Monitoring of effectiveness is required for autoclaves for every run by using either electronic probes and data recorders or printers, or using indicator strips, both of which need to be kept for records.
Emergencies
- Emergency procedures should be prepared in advance for dealing with accidents and incidents.
- Emergency procedures should be determined in risk assessments and set out in standard operating procedures.
- Names and contact details of principal investigators, responsible persons, biological safety supervisors, health, safety and wellbeing coordinators should be available in laboratory.
- First aid facilities should be provided.
- Workers must understand and be able to implement emergency procedures.
- Assess the accident or emergency before deciding and taking any action.
- Inform others of accidents and isolate the area or evacuate if required.
- Seek assistance and use PPE if required.
- Seek first aid and medical treatment if required.
- Individuals involved in serious incidents or where there is uncertainty should be referred or sent to hospital for clinical assessment and treatment.
- Decontaminate the work area or laboratory after an accident or emergency.
- Report accidents and emergencies immediately to supervisors or managers and Corporate Health and Safety.
- Report accidents and emergencies immediately practicable.
- Refer injured persons for an occupational health assessment where required.
Spills
- Emergency procedures should be prepared in advance for dealing with spillages and releases.
- Emergency spillages and release procedures should be determined in risk assessments and set out in standard operating procedures.
- Instructions, spills kits and PPE should be provided.
- Instructions should be provided on laminated sheet near equipment where required.
- Notify other workers and isolate area (if required).
- Evacuate laboratory if risk of airborne infection.
- Allow aerosols to settle.
- Contain spillages with tissues or granules where required.
- Cover with suitable disinfectant liquid or granules where required.
- Allow sufficient contact time before clean up.
- Clean up debris gently and do not use a brush.
- Pick up broken glass carefully (eg forceps or swabs).
- Put debris in a suitable waste or sharps container for safe disposal.
- Disinfect contaminated surfaces and equipment.
Personal Contamination
- Remove contaminated clothing as quickly as possible and leave in laboratory.
- Remove contamination from skin, eyes and mouth by thorough washing with water.
- Minor cuts and small puncture wounds should be encouraged to bleed.
- Wash wounds with soap and water.
- Dress wounds.
- Use PPE if required when helping injured persons.
- Seek help where required including where relevant first aid or hospital.
- Emergencies should be sent straight to hospital and call ambulance if necessary.
- Explain incident and biological agents or hazards or genetically modified organisms to medical staff.
- Report all accidents immediately or as soon as practicable.
Information, Instruction, Supervision and Training
- Information should be provided to all workers on hazards, risks, control measures, monitoring, health surveillance etc.
- Instructions should be provided to all workers on actions and precautions to be taken, use, storage, transport, disposal, emergency procedures etc.
- Training should be provided to all workers on detailed and effective application of control measures etc.
- All workers must be adequately trained and supervised.
Containment Level 2
Introduction
Containment level 2 (CL 2) is used for work with medium risk biological agents and hazards, genetically modified organisms, animals and plants. This guidance is a summary of some important controls used for work in containment level 2 laboratories but is not exhaustive and you will need to do other things as well depending on your specific work and risk assessments. It is not intended to describe all of the necessary control measures and more information on controls can be found on the SEPS, HSE and DEFRA websites. For containment level 2 work, all requirements in containment level 1 must be met with the following requirements specific to level 2 containment work.
General Safety
All requirement of containment level 1 and:
- Laboratory should consist of a lobby and laboratory.
- Laboratory should contain its own equipment (so far as reasonably practicable).
- Laboratory Should be sealable to permit fumigation.
- Laboratory should be separated from other activities in building.
- Laboratory should have adequate ventilation and temperature control.
- Suitable means of communication should be provided (eg phones and computers etc).
- Suitable means of detection and warning of emergencies should be provided (eg fire detection/alarms, and gas monitors/alarms etc).
- Observation windows or alternative (eg CCTV) means of viewing occupants should be provided.
- Effective inward airflow and negative pressure must be maintained and extracted exhaust air must be HEPA filtered before discharge.
- Air supply and extract systems should be interlocked and using other means of control to prevent positive pressurisation.
- Air extracts and inputs should not interfere with microbiological safety cabinet performance.
- Laboratory ventilation and safety cabinets should be regularly inspected, maintained and tested usually at least every six months.
- Laboratory sealability must be validated at least every twelve months.
- Validated standard fumigation and emergency fumigation procedures are required.
- Handwash sink with an emergency eyewash hose should be near to all exit doors of lobby and laboratory.
Personal Protective Equipment (PPE)
All requirement of containment level 1 and:
- Gloves must be worn for all work
- Gowns should be stored in laboratory.
- Gowns should be autoclaved before laundering or disposal.
Spills
All requirement of containment level 1 and:
- Minor spillages may be decontaminated using disinfectants.
- Major spillages require evacuation and fumigation of laboratory.